Mastering Chiller Efficiency: Tips Every Facility Manager Should Know
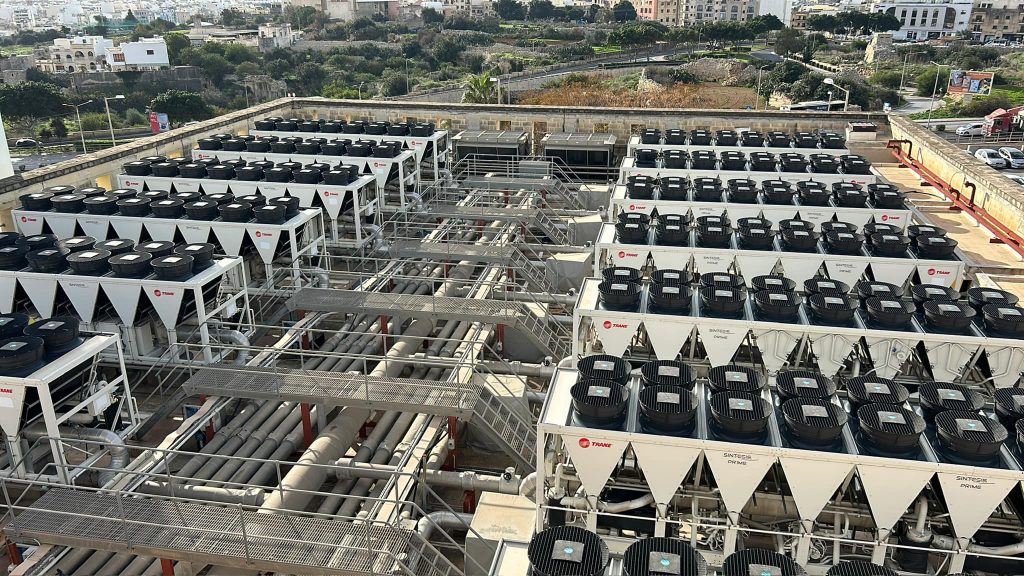
Introduction
Did you know that a single malfunctioning chiller can increase your facility’s energy costs by 27%?
Here’s how to make sure yours runs smoothly all year round. In this post, we will give you insight into the secrets to maintaining efficient and cost-effective chiller plant operations, ensuring you’re always running as smooth as possible, and keep your operating costs to a minimum.
Understanding Chillers
Chillers are a critical component in various industries, from HVAC systems to manufacturing processes. They work by removing heat from a liquid via a vapor-compression or absorption type refrigeration cycle. This cooled liquid can then be used to cool air or equipment as needed.
What are some common chiller problems?
Refrigerant Leaks
Refrigerant leaks are a very common issue that can lead to massive inefficiencies and increased energy costs in your chiller plant. Leaks can occur due to poor maintenance, corrosion, or physical damage to the chiller components. If you want your building to run smoothly, then you need to make sure that your chiller is leak free, and your chiller is properly charged.
Fouled Tubes
Over time, chiller tubes can become fouled with scale, algae, or other contaminants, reducing heat transfer efficiency and causing the chiller to work harder and consume more energy. It is extremely important that you are cleaning the condenser tubes and condenser coils (if its and air cooled chiller) at least one time annually.
Inadequate Maintenance
Neglecting regular maintenance can lead to a host of problems, including reduced efficiency, higher energy costs, and unexpected breakdowns. A chiller is a mechanical piece of equipment, just like a car. If you didn’t change the oil in your car, or maintain it any any way for 5-10 years it will break down, and will cost substantially more than an oil change and a little TLC would.
The Juice Factory:
I worked with a facility manager at a juice factory, who was at his wits’ end with constant chiller breakdowns. They were having breakdowns every month, and each failure not only disrupted day to day operations but also dramatically raised his operating costs. After a thorough inspection, we found multiple issues, including fouled tubes lots of refrigerant leaks, and some controls problems. After getting all of the repairs made, we started doing maintenance for them, and after 1 year, they haven’t had any dramatic costs associated with their chiller in 2 years.
Chiller Maintenance Tips
To keep your chillers running efficiently, do these the these things.
Regular Inspections:
Schedule routine inspections to catch issues early before they cost five times as much.
An Example would be: Regularly inspect and clean condenser coils, and clean condenser tubes to prevent buildup and ensure optimal performance.
Monitor Refrigerant Levels:
Ensure refrigerant levels are adequate and there are no leaks.
Tip: Use electronic leak detectors for accurate detection of leaks.
Clean The Chiller Tubes:
Periodically clean the chiller tubes (typically one time annually on the condenser, and every 5 on the evaporator, to prevent fouling.
Tip: Use mechanical or chemical cleaning methods depending on the type of buildup.
Check Water Treatment:
Ensure proper water treatment to prevent scale and corrosion in the system.
Tip: Find a good water treatment provider for helping you maintain the correct chemistry in the water in the chiller
Upgrades:
Variable Speed Drives (VSDs):
VSDs adjust the speed of the chiller’s compressor to match the cooling load you need, and also help during startup so you don’t get billed for large peaks in power.
If you are able to lower the compressors speed by 20% during lower load conditions, you can save 50% on your power consumption.
This results in significant energy savings and reduced wear and tear on the system.
Magnetic Bearing Compressors:
These compressors offer higher efficiency and reliability by reducing friction and wear. They also operate more substantially more quietly and require less maintenance compared to traditional compressors. but buyer beware, a lot of these are throw away compressors, and cant be rebuilt. As a result, they are essentially maintenance free, but if they do fail, it will cost you a fortune because you will need to replace the entire compressor.
Pannel (Controls) Upgrades:
Some times it makes sense to upgrade the chillers control panel. Old control panels may not be available, and it is much more cost effective to do an upgrade. with the upgrade, comes a lot of extra features, that enables the startup technician to dial your system in, and operate at peak efficiency.
Want To Learn More About Air Cooled Chillers And Chiller Systems?
Join the thousands of professionals working in the chiller industry around the world to share knowledge, learn from each others experiences, and help each other find custom solutions to complex problems in the chiller industry!
Responses